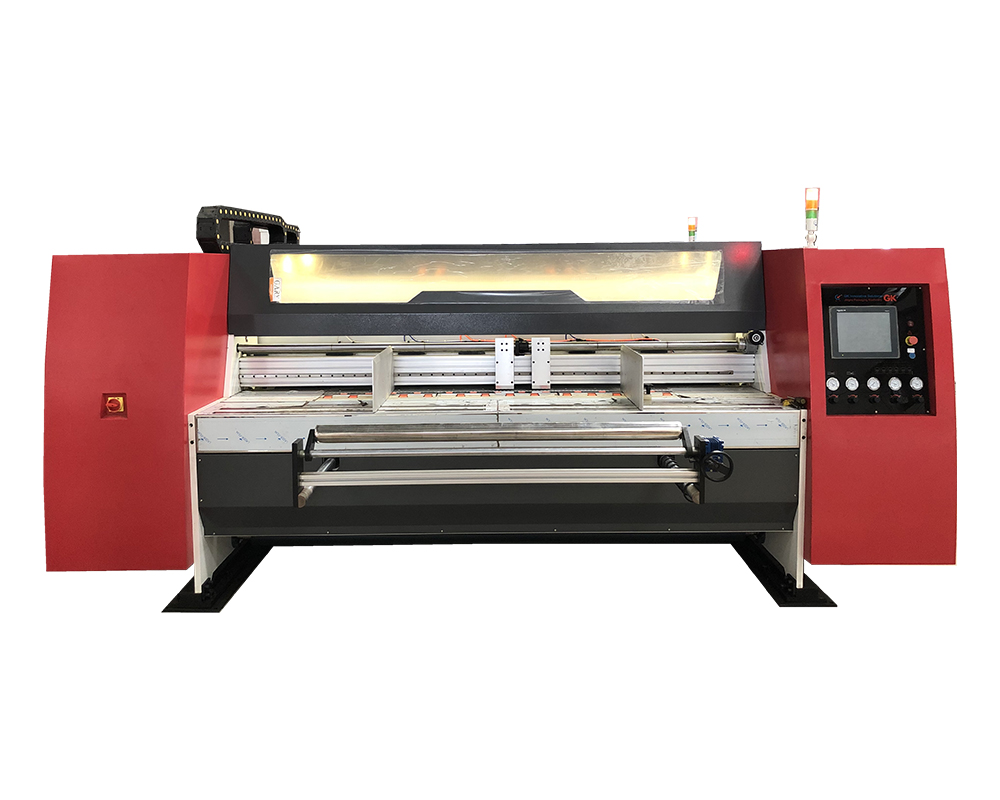
Small Corrugated Box Making Machine
Carton Forming Machine
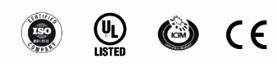
-
+86-13702592807 WhatsApp
-
sales@jingoupack.com Email
Small Corrugated Box Making Machine is a mechanical equipment specially used for producing small corrugated boxes.
Small Corrugated Box Making Machine Parameter
Model | CK25 |
Max.feeding Size(W*L) | 2500mm*unlimited |
Min.feeding Size(W*L) | 120*350mm |
Die-Cut Size(W*L) | 140*700mmx2pcs |
Slotting Width | 7mm |
Max.slotting Depth | 500mm |
02xx Max.box Height | 1600mm |
02xx Min.box Height | 100mm |
Max.angle Cutting Width | 45mm |
Feedng Thickness | 2-11mm |
Speed | 400-600pcs/h |
Air Pressure | 0.3-0.6Mpa |
Total Motor Power | Abt15kw |
Dimension(W*L*H ) | 4050*700*2000mm |
Overall Net Weight | Abt8000kg |
Advantages of Small Corrugated Box Making Machine
Diverse feeding sizes
The maximum feeding size: the width and length can reach 2500mm, which enables it to handle larger corrugated cardboard and meet the diverse needs of different customers for carton sizes. Whether it is a larger transport box or a slightly larger product box, it can be easily handled.
The minimum feeding size: the width is 120*350mm. For small-sized cartons required for some small and delicate products, it can also be accurately fed and processed, reflecting its flexibility in size processing.
Accurate cutting and slotting capabilities
Die-cutting size: the width and length can reach 140*700mm, and the maximum cutting width can reach 45mm. It can accurately die-cut corrugated cardboard to ensure that the cutting edges are neat and smooth, providing a good foundation for subsequent carton forming.
Slot width: 7mm slot width and maximum slot depth of 500mm enable various slot operations on cartons to achieve high precision and meet the slotting requirements of cartons of different designs and structures, such as various slot lines for easy folding and assembly.
Wide range of feed thickness adaptation
It can handle corrugated cardboard with a thickness of 2-11mm. Whether it is thinner single-layer corrugated cardboard or thicker multi-layer corrugated cardboard, it can be smoothly fed and processed on this machine, which greatly expands the types of corrugated cardboard it is suitable for and can meet the production needs of cartons of different strengths and uses.
Efficient production speed
The speed can reach 400-600pcs/h. Such a production speed is at a high level among small corrugated box manufacturing machines. It can produce a large number of cartons in a short time, effectively improving production efficiency, and is especially suitable for order production with certain batch requirements.
Moderate power and air pressure requirements
Total motor power: about 15kw, which is relatively moderate. While ensuring stable operation of the machine and sufficient power output, it will not cause excessive energy consumption, which helps to reduce production costs.
Air pressure: 0.3 - 0.6Mpa. Such air pressure requirements are easier to meet in general industrial production environments. No special high-pressure air source configuration is required, which facilitates the installation and use of the machine.
Reasonable size and weight design
Dimensions: Width, length and height are 4050*700*2000mm. The overall structure is compact and will not take up too much factory space. It is more friendly to production sites with limited space.
Total net weight: about 8000kg. Under the premise of ensuring the stability and firmness of the machine, the weight is controlled within a reasonable range. It will not cause problems such as factory floor load due to excessive weight, and it can also ensure the stability of the machine during operation.
Application of Small Corrugated Box Making Machine
Application in the food industry
Small Corrugated Box Making Machine helps the packaging needs of the food industry. Food companies need a large number of small corrugated boxes of different specifications to package various foods. The ability to quickly produce suitable cartons and print brand logos on them can help enhance the image and recognition of food brands, attract consumers' attention on supermarket shelves, and promote product sales.
Application in the electronics and electrical industry
In the electronics and electrical industry, small corrugated box making machines also play an important role. They can effectively protect the safety of these sophisticated electronic and electrical products during transportation, prevent them from being damaged by shaking during transportation, and help enhance consumers' trust and favorability in the brand and enhance the market competitiveness of products.
Application in the cosmetics industry
The cosmetics industry has high requirements for packaging. It not only focuses on protecting products, but also attracts consumers in appearance. It helps cosmetics stand out from many competing products and attracts consumers to buy. At the same time, the stable carton structure can also ensure the safety of fragile cosmetics such as perfumes packaged in glass bottles during transportation and sales.
Application in the pharmaceutical industry
In the pharmaceutical industry, small corrugated boxes are used to package some small medicines, health products, etc., which helps the standardized management of pharmaceutical products and the correct use of consumers, and also helps pharmaceutical companies meet relevant regulatory requirements and improve the compliance and image of the company.
Care and Maintenance of Small Corrugated Box Making Machine
Daily cleaning and maintenance
Cleaning of the machine body surface: After the production is completed every day, use a clean soft cloth to wipe the machine body surface to remove dust, paper scraps and other debris. For stubborn stains, you can use a mild detergent to wipe, but avoid the detergent from entering the inside of the machine. After wiping, wipe it with a dry cloth to prevent rust.
Cleaning of the feed and discharge ports: Check whether there is cardboard residue or blockage at the feed and discharge ports. If so, clean them in time to ensure smooth feeding and discharging. You can use tools such as brushes to clean debris in the gaps.
Cleaning of cutting and slotting parts: Clean the cutting tool and slotting mold regularly to remove paper scraps and glue residues on them. Use a special tool cleaner to wipe to maintain the sharpness of the tool and the accuracy of the slotting mold.
Lubrication and maintenance
Lubrication of transmission parts: The transmission chain, gears and other parts of the machine need to be lubricated regularly. Add lubricating oil every 1-2 weeks according to the frequency of use of the machine. Select a suitable industrial lubricant and add it according to the requirements of the operation manual to ensure smooth operation of the transmission parts and reduce wear.
Bearing lubrication: Check the lubrication of each bearing and add grease every 2-3 months. Use high-quality high-temperature grease to avoid bearing overheating and damage due to insufficient lubrication.
Electrical system maintenance
Line inspection: Check the electrical circuit once a month to see if it is loose, damaged or aged. For loose wiring, tighten it in time; for damaged lines, replace it in time to prevent electrical failures and safety accidents.
Electrical component inspection: Check the working status of electrical components such as contactors and relays to see if there is abnormal heating, contact ablation, etc. If there is a problem, replace the electrical components in time to ensure the stable operation of the electrical system.
Mechanical structure inspection
Screw and nut tightening: Check the screws and nuts on the machine every week to see if they are loose, especially the screws in key parts such as cutting parts and transmission parts. If there is any looseness, tighten it in time to prevent the machine from vibrating more and parts from being damaged due to loose screws.
Machine level adjustment: Check the levelness of the machine regularly and measure it with a level. If the machine is not level, it will affect the accuracy of cutting and slotting. The anchor bolts of the machine need to be adjusted to make the machine level.
Tool and mold maintenance
Tool sharpening: When the sharpness of the cutting tool decreases, it needs to be sharpened. According to the material and wear of the tool, choose the appropriate sharpening method and tool. After sharpening, test cutting should be carried out to ensure that the cutting effect meets the requirements.
Mold storage: For slotting molds that are not used temporarily, they should be properly stored. After cleaning, apply anti-rust oil and place them in a dry and ventilated place to prevent rust and damage to the mold.
Regular calibration and debugging
Dimension calibration: Calibrate the cutting size, slotting size, etc. of the machine every quarter. Use standard measuring tools to measure and compare with the set size. If there is a deviation, adjust it according to the method in the operation manual to ensure that the size of the produced carton is accurate.
Pressure and speed debugging: According to the thickness and material of the corrugated cardboard, regularly adjust the pressure and speed of the machine. Ensure that the machine can operate stably under different working conditions to improve production efficiency and product quality.
Jingou packaging machinery Co.,ltd
Jingou is a high-tech enterprise with forward thinking special designed,manufacturer of corrugated carton machine for small quantity orders .We had developed a very first auto thin slitter scorer machine which you can not find all over the world in 2009.And we keep working on developing functional box maker machine CK25 which earn many invention patents and utility model patents and passed CE certifications .Jingou machine had completed changed the low efficiency production mode of small quantity orders to meet the true needs of customers .